CUTTING EDGE INNOVATION AND TECHNOLOGY,
TO BE COMPETITIVE ALL OVER EUROPE
TECNOLOGY
For over 30 years, no-one had built a foundry from scratch in Italy. They generally just expanded existing ones.
The Dalli Cani family not only decided to build a completely new foundry. It also decided to use the best constructors on the market, entrusting the entire project to them. That is why the entire structure was purchased from the Danish company DISA, considered and acknowledged as the best producer in the world for foundry plants and structures.
During the design stage, they considered all the needs presented by their historical Dalli Cani foundry employees, some with 30 years foundry experience. The result is the latest DisaMatic 130 plant; unique in Europe for certain aspects.
A 6000m2 surface, a 24 ton daily production capacity, with care over each single detail; so much so that the plant’s earth plant’s mixer is fully covered in ceramics, to be extremely efficient.
This care for detail always provides excellent results; as if in formula 1, though having an excellent car, the difference was made by a special petrol mix.
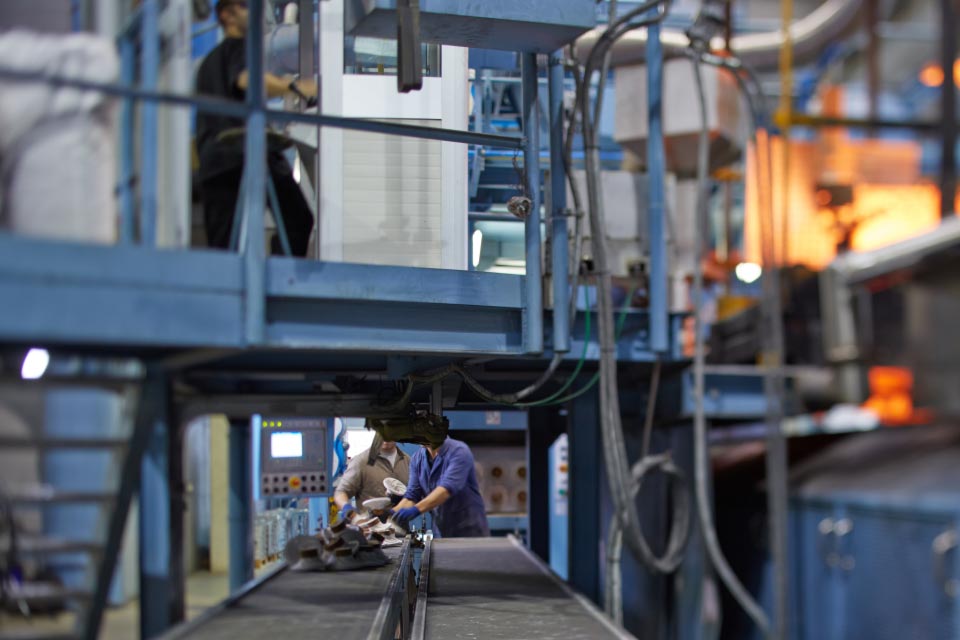
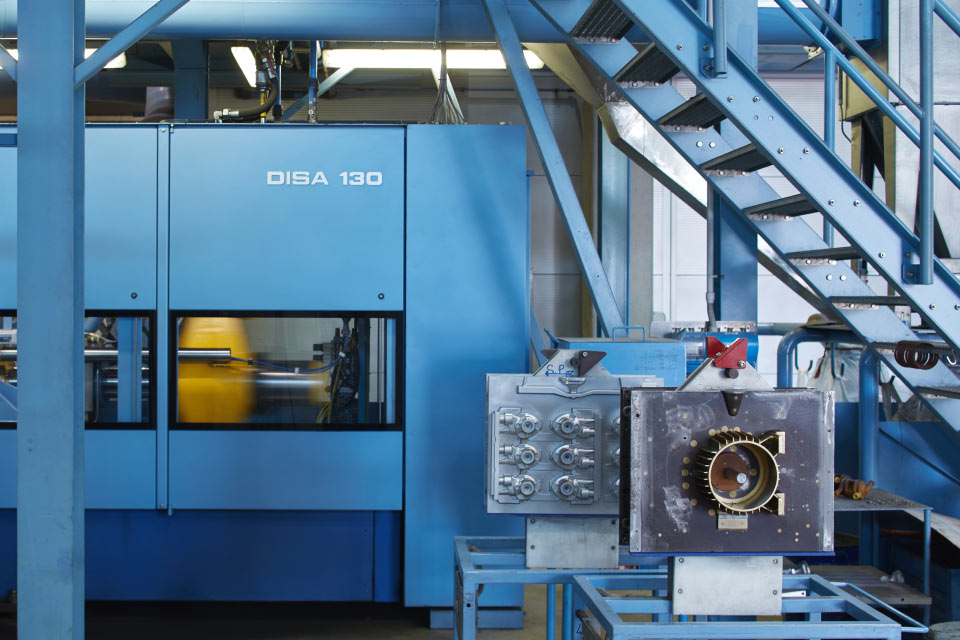
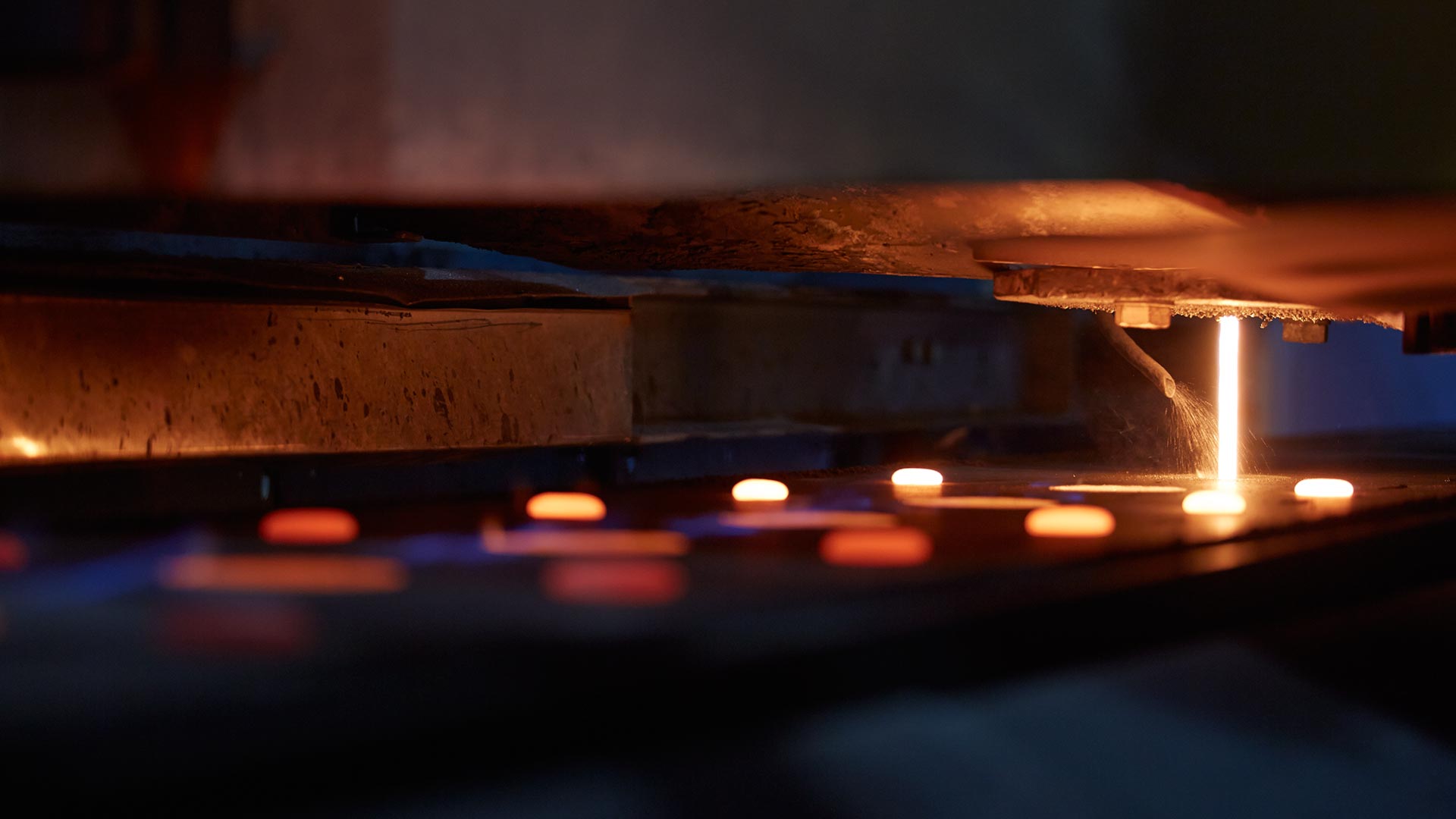
But the care over cutting edge technology does not end with the smelting plant.
The laboratory used to test materials is of considerable importance. It enables constant monitoring of the quality of cast iron produced, and the fully automated warehouse, with 3200 positions.
The warehouse is the real feather in the GDC Cast cap. Our clients’ models are protected both physically – the warehouse is indoors so protected against external agents – and intellectually – thanks to this technology single clients are hidden from view and intellectual property is protected.
This technological difference compared to most competitors makes GDC Cast a foundry that can meet all client needs. A foundry maximising production, with a top efficiency level and reduced costs; a flexible production foundry, equally versatile when producing large and small numbers and able to concentrate on what’s essential: melting.
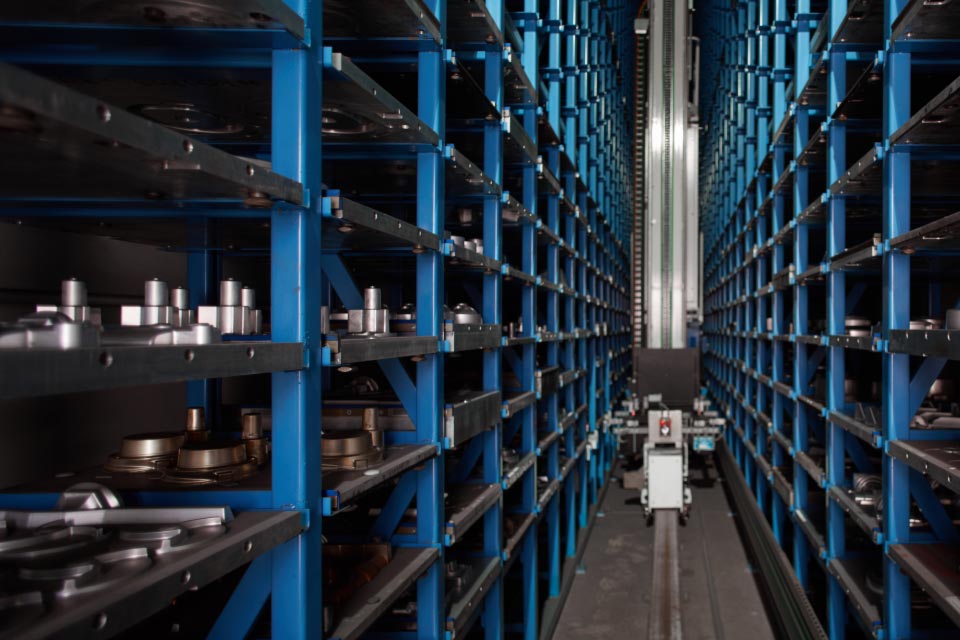
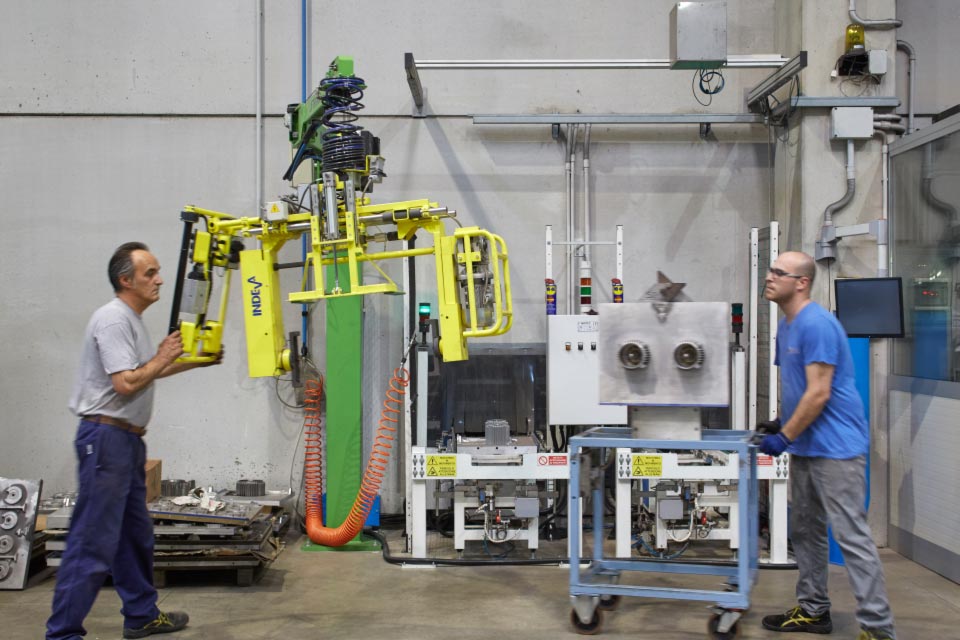